Meet Norman Bodek, the Oregon-based early LEAN manufacturing champion
Norman Bodek began exploring the notion of productivity in the 1970s. As he pored more deeply into the topic, and how it affected manufacturing, he found himself increasingly analyzing ideas that were born overseas.
Along the way, he became one of the first Americans to write about “lean manufacturing, the processes honed in Japan that were used, to worldwide acclaim, to build Toyota vehicles. He did so by transcribing the theories from a spot on Northeast Sandy Boulevard. And he became perhaps America’s foremost expert on Lean.
Lean theorists hold that manufacturing can be done more efficiently without sacrificing quality. The concept has been adopted and adhered to by many in Portland’s Maker community.
Bodek spoke before the appropriately named group Lean Portland in early December. The full 1:44 presentation is below (the video’s by Rose City Digital Marketing & Lean Portland).
Before his talk, we caught up with the 85-year-old Bodek to learn more about the systems he embraced in the 1970s — and how they apply to American ingenuity today.
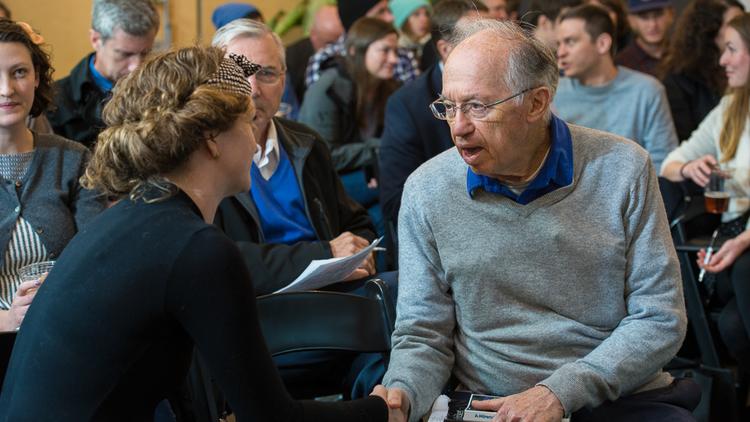
Norman Bodek appeared at the Lean Portland event in early December. Image by PhotosByKim.com
Is the notion of Lean in 2017 where you expected it to be when you started the transcription work? When I started in the year 1979, I was on a search to discover what the Japanese were doing in quality and productivity. They were leading the world at the time. Luckily, serendipitously, I went to Japan and led a study mission with 19 senior executive managers who were subscribers to my newsletter, Productivity, and we were introduced to the Toyota Production System. I was fascinated with it and most fortunately met Dr. Shigeo Shingo, an independent consultant, and Taiichi Ohno, senior vice president of manufacturing and was fortunate enough to translate and publish their books into English.
Prior going to Japan, I visited an Oldsmobile plant in Tarrytown, New York, which gave me an opportunity to see the differences when I visited Toyota. Toyota was light years ahead. It was obvious even for me who had no prior experience in manufacturing. The work was done much faster. While Oldsmobile had 1000 parts for the thousand cars to be manufactured that day, I saw only a minimal amount of inventory, only 18 engines for example sitting on the floor.
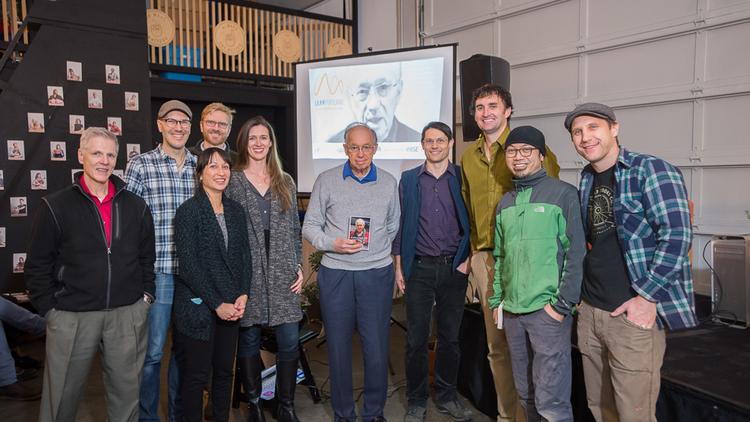
Bodek continues to nurture many fans of both him as well as the Lean principles. Image by PhotosByKim.com
From my perspective, there are very few companies in America now some 35 years later who really understand what the Toyota Production System or what we call Lean really is. Most companies implement a few of the Lean tools and do get some results but often they just say Lean does not work for me. Yes, Lean is all out war against wastes of inefficiency. Ohno came up with seven wastes and I added two: the underutilization of people’s talents and managers resistance to change. A manager’s job is primarily to develop people, but here often with Lean efforts, we lay off people when they make improvements for us and we rarely ever develop people to their maximum creative potential. It is foolish. For when you develop people, and they are our most important asset, you can grow your organization exponentially.
I still take people to Japan, even though I’m 85 years old because they ask me to. In fact, I hope to go again in March next year and also in June because it is an unending discovery process to look at what the best in the world are doing and to get an opportunity to see firsthand and be able to come back and do it yourself.
About 100 or so turned out for Bodek’s Lean Portland appearance. Image by PhotosByKim.com
And that ninth waste, is what prohibits most companies from being successful. In addition to developing people, a manager should be leading change not preventing it. I teach, and I will talk more about the Harada Method on December 6th in Portland. I had one student over zoom.us who I was teaching how to develop a very strong goal and to work out the detailed tasks to attain it. He loved what I was teaching. I asked him, “pay me something.” He said, “I will have to ask the president of my hospital.” I told him before, call Joe Schwartz at the Baptist Memorial Hospital in Indianapolis and ask him how much he saved at hospital system. He did and Joe told him they saved over one and a half million dollars. This student then went to the president of his hospital and asked for some money and the president said, “we have no money in the budget.”
In 1983, Nummi was set up by a joint venture between General Motors and Toyota. Toyota did it to teach General Motors their production system. This plant actually was the worst plant that General Motors had, but one year later under Toyota leadership it became the best plant that General Motors had. Unfortunately, General Motors could not replicate it and a few years later General Motors went bankrupt.
When I first met Mr. Ohno, Toyota was not too happy to share their information with the West, but Ohno realized that others would not be able to really replicate what they did in Japan.
To summarize your question, no. I would have hoped that American industry would be much smarter to recognize the gift that Toyota has given us. After World War II, the Japanese sent over thousands of people to study American manufacturing. They took pictures of everything. They replicated in Japan. They were known as a nation of copiers. And then they improved it and became one of the most advanced societies in the world. Just go with me in June and see with your own eyes.
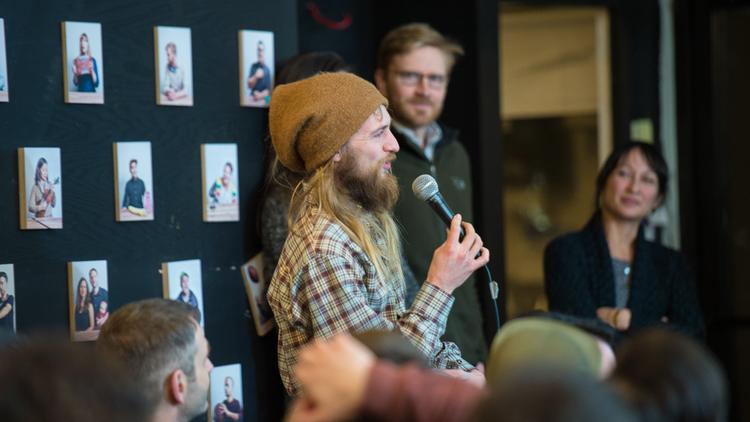
Bodek’s appearance sparked much interest from the city’s Makers.
What sector has used it the best (i.e. is it necessarily the manufacturing or industrial world)? I mean, thousands or tens of thousands of companies and hospitals are attempting to bring aspects of lean into their organization but without true dedication and getting everybody involved; it just isn’t happening to the extent that it should. There is an enormous thrust in America to bring in robots. I’m not against robots but it is much less expensive to develop people and it helps create a better society. What I especially like in Japan today, is the emphasis on switching from repetitive boring manufacturing to fostering people to become masters, craftspeople. Where we have people doing the same repetitive task every few minutes, Canon has a supermeister who makes the entire copier all by herself in three hours. Imagine the sense of self-respect that she has.
Are there any particulars about Portland, be it spirit or industriousness, that mean the notion is applied better by companies here? Portland is a great city. A wonderful place to live. Homeless, however, just tarnishes Portland’s image. If Portland could solve the homeless problem, and I would love to help, it would even be so much better. Portland is one of the best places in America to really bring the Lean into full application. It is not that difficult. It doesn’t require magic. It just requires a deeper understanding of what it means.
Are there any reasons the philosophies or practices of lean would be affected in the post-Trump world? I would love to talk about politics, but it would only get me into trouble. Instead of looking at our political world, each person should be looking at themselves and seeing what they can do to become a master, a highly skillful person, at something that other people value. You grow and the world gets better.
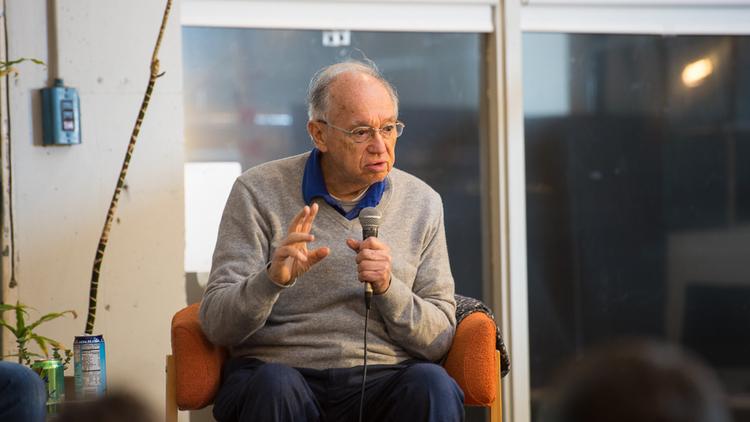
Bodek believes the principles can move beyond industry. He hopes someone can apply them to finding solutions to homelessness. Image by PhotosByKim.com
It really does seem, as you noted earlier, it can be applied to any way of thinking. Around seven years ago, when I was teaching at Portland State University, four students asked to intern with me. I asked a good friend of mine, a former author of mine, Shigehiro Nakamura, to help me teach the students the best of Japanese management. We would meet on Skype every other week. Around the fifth or sixth week we were talking about standard work and were introduced to day-to-day management by Takashi Harada. Mr. Harada developed a method to teach people how to be “champions.” He took students at the worst junior high school in Osaka and 12 of them won 13 gold medals in track and field. They were the best athletes at their age and all of Japan. It never happened before.
Mr. Harada then went out to industry and has taught 80,000 people in Japan his method. I became fascinated and I went to Japan to meet him, eventually co-authored a book with him and taught the method here in Portland. I am thrilled what people are capable of doing when they pick a strong goal and work out specific tasks to attain that goal. I would hope that some of these are people interested not only in Lean but getting the homeless off the streets.